Destylacja rozpuszczalników to proces, który polega na oddzieleniu składników mieszaniny na podstawie różnic w ich temperaturach wrzenia. Jest to jedna z najstarszych i najważniejszych metod stosowanych w chemii oraz przemyśle chemicznym. Proces ten można przeprowadzać na różne sposoby, w zależności od charakterystyki substancji, które chcemy oddzielić. W destylacji prostej, mieszanina jest podgrzewana, a para powstająca z cieczy przechodzi przez chłodnicę, gdzie skrapla się z powrotem do postaci cieczy. W przypadku destylacji frakcyjnej, stosuje się kolumny frakcyjne, które pozwalają na bardziej efektywne oddzielanie składników o zbliżonych temperaturach wrzenia. Kluczowym elementem tego procesu jest dobór odpowiednich warunków, takich jak ciśnienie i temperatura, co ma istotny wpływ na wydajność destylacji.
Jakie są zastosowania destylacji rozpuszczalników w przemyśle
Destylacja rozpuszczalników ma szerokie zastosowanie w różnych gałęziach przemysłu. W przemyśle chemicznym jest wykorzystywana do oczyszczania substancji chemicznych oraz do separacji składników mieszanin. Na przykład, w produkcji alkoholu etylowego, proces ten pozwala na uzyskanie czystego produktu poprzez usunięcie niepożądanych zanieczyszczeń. W przemyśle farmaceutycznym destylacja jest kluczowa dla produkcji wysokiej jakości leków, gdzie czystość substancji czynnych jest niezwykle istotna. Ponadto, w przemyśle petrochemicznym destylacja frakcyjna jest używana do separacji różnych frakcji ropy naftowej, co umożliwia produkcję benzyny, oleju napędowego oraz innych produktów naftowych. Również w laboratoriach analitycznych destylacja jest często stosowana do przygotowywania próbek do dalszych badań.
Jakie są różnice między destylacją prostą a frakcyjną
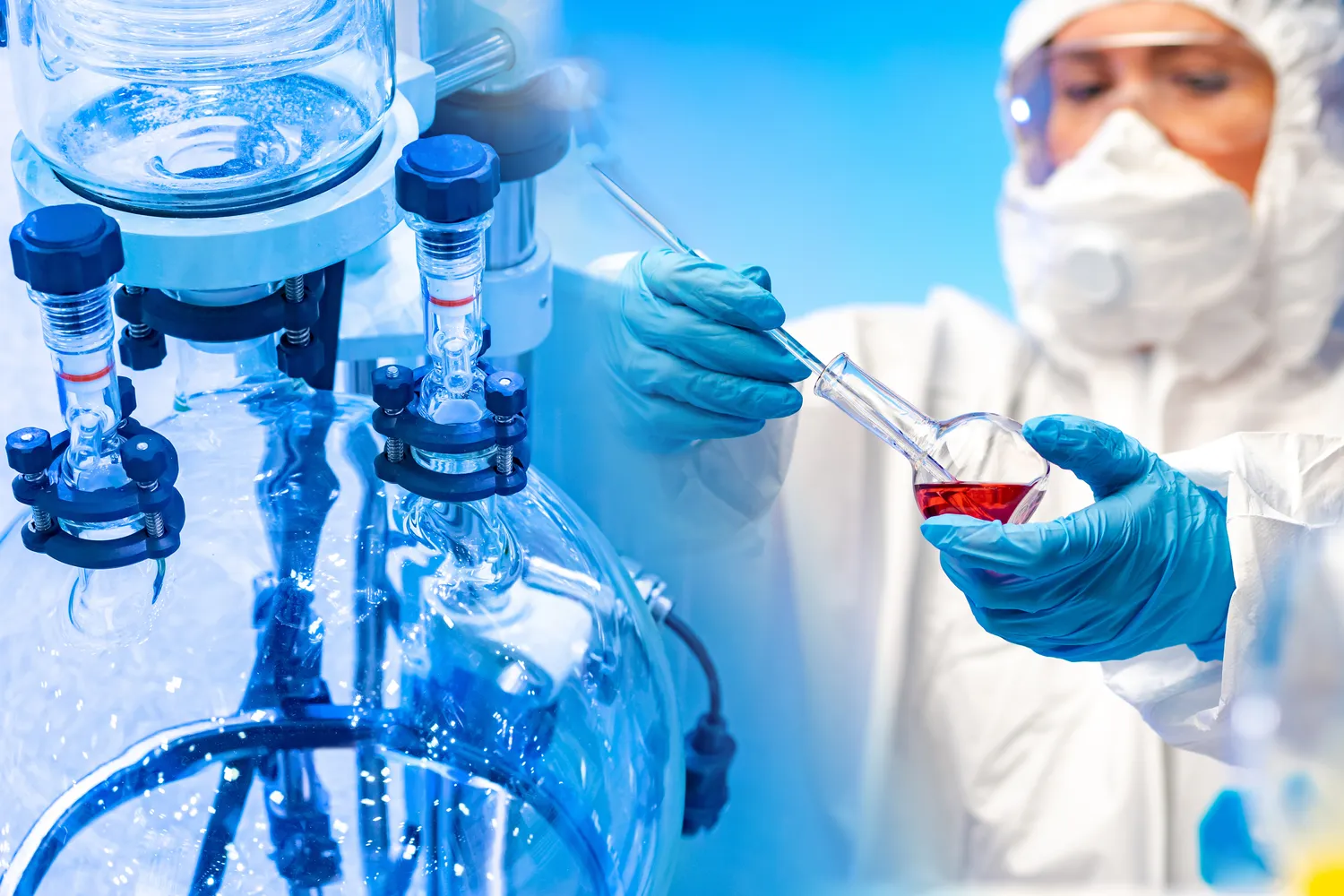
Destylacja prosta i frakcyjna to dwa podstawowe rodzaje procesów destylacyjnych, które różnią się zarówno techniką wykonania, jak i zastosowaniem. Destylacja prosta jest najczęściej stosowana do separacji substancji o znacznie różniących się temperaturach wrzenia. Proces ten polega na podgrzewaniu cieczy i zbieraniu pary skraplającej się w chłodnicy. Jest to metoda stosunkowo łatwa i szybka, jednak nieefektywna w przypadku mieszanin o zbliżonych temperaturach wrzenia. Z kolei destylacja frakcyjna wykorzystuje kolumny frakcyjne, które umożliwiają wielokrotne skraplanie i parowanie składników mieszaniny. Dzięki temu możliwe jest uzyskanie wyższej czystości produktów oraz lepsza separacja substancji o podobnych właściwościach fizycznych. W praktyce wybór metody zależy od specyfiki procesu oraz wymagań dotyczących czystości końcowego produktu.
Jakie urządzenia są używane do destylacji rozpuszczalników
W procesie destylacji rozpuszczalników wykorzystywane są różnorodne urządzenia, które mają na celu zapewnienie efektywności oraz bezpieczeństwa całego procesu. Podstawowym urządzeniem jest aparat destylacyjny, który może mieć różne formy w zależności od rodzaju destylacji. W przypadku destylacji prostej najczęściej stosuje się prosty zestaw składający się z kolby grzewczej, chłodnicy oraz naczynia odbierającego skroploną ciecz. W przypadku bardziej skomplikowanej destylacji frakcyjnej konieczne są kolumny frakcyjne wyposażone w różnego rodzaju elementy zwiększające powierzchnię kontaktu między parą a cieczą, co sprzyja lepszemu oddzieleniu składników. Dodatkowo nowoczesne technologie pozwalają na automatyzację procesu oraz monitorowanie parametrów takich jak temperatura czy ciśnienie za pomocą specjalistycznych czujników i systemów sterujących.
Jakie są zagrożenia związane z procesem destylacji
Proces destylacji rozpuszczalników wiąże się z pewnymi zagrożeniami zarówno dla osób prowadzących te operacje, jak i dla środowiska naturalnego. Przede wszystkim podczas podgrzewania substancji mogą powstawać niebezpieczne opary chemiczne, które mogą być toksyczne lub łatwopalne. Dlatego tak ważne jest zapewnienie odpowiedniej wentylacji oraz stosowanie środków ochrony osobistej przez pracowników zajmujących się tym procesem. Ponadto niewłaściwe prowadzenie procesu może prowadzić do niekontrolowanego wzrostu ciśnienia wewnątrz aparatu destylacyjnego, co stwarza ryzyko wybuchu lub pożaru. Kolejnym zagrożeniem jest możliwość kontaminacji produktów końcowych przez niepożądane substancje chemiczne obecne w surowcu wyjściowym lub wynikające z reakcji zachodzących podczas procesu.
Jakie są kluczowe etapy procesu destylacji rozpuszczalników
Proces destylacji rozpuszczalników składa się z kilku kluczowych etapów, które są niezbędne do skutecznego oddzielania składników mieszaniny. Pierwszym krokiem jest przygotowanie surowca, który może obejmować filtrację lub oczyszczanie, aby usunąć zanieczyszczenia, które mogłyby wpłynąć na jakość końcowego produktu. Następnie następuje podgrzewanie cieczy w kolbie destylacyjnej. W tym etapie ważne jest, aby kontrolować temperaturę, aby uniknąć przegrzania lub niekontrolowanego wrzenia. Kiedy ciecz osiągnie swoją temperaturę wrzenia, para zaczyna unosić się do góry i przechodzi przez chłodnicę, gdzie skrapla się z powrotem do postaci cieczy. Kolejnym krokiem jest zbieranie skroplonego produktu w odpowiednich naczyniach. W przypadku destylacji frakcyjnej proces ten jest bardziej złożony, ponieważ wymaga wielokrotnego parowania i skraplania w kolumnach frakcyjnych. Ostatnim etapem jest analiza jakości uzyskanych produktów oraz ich ewentualne dalsze przetwarzanie lub pakowanie.
Jakie są najczęstsze błędy popełniane podczas destylacji
Podczas przeprowadzania procesu destylacji rozpuszczalników mogą wystąpić różnorodne błędy, które mogą negatywnie wpłynąć na efektywność oraz bezpieczeństwo operacji. Jednym z najczęstszych błędów jest niewłaściwe ustawienie temperatury grzania, co może prowadzić do niepełnej separacji składników lub ich degradacji. Zbyt wysoka temperatura może spowodować przegrzanie cieczy, a zbyt niska może uniemożliwić osiągnięcie wymaganej temperatury wrzenia. Innym powszechnym problemem jest niewłaściwe dobranie aparatury destylacyjnej do rodzaju mieszaniny, co może skutkować niską wydajnością procesu. Ważne jest również, aby regularnie kontrolować ciśnienie wewnątrz aparatu destylacyjnego, ponieważ jego wzrost może prowadzić do niebezpiecznych sytuacji. Dodatkowo, brak odpowiedniej wentylacji w miejscu pracy może zwiększać ryzyko wystąpienia oparów toksycznych substancji chemicznych.
Jakie są różnice między destylacją a innymi metodami separacji
Destylacja rozpuszczalników to jedna z wielu metod separacji składników mieszanin chemicznych, ale różni się od innych technik pod względem zasad działania oraz zastosowania. Na przykład, ekstrakcja to metoda polegająca na rozpuszczeniu jednego lub więcej składników w odpowiednim rozpuszczalniku, co pozwala na ich oddzielenie od reszty mieszaniny. W przeciwieństwie do destylacji, ekstrakcja często nie wymaga podgrzewania i może być stosowana do substancji o niskich temperaturach wrzenia. Inną popularną metodą separacyjną jest chromatografia, która wykorzystuje różnice w powinowactwie składników do różnych faz (stałej i ciekłej) w celu ich oddzielenia. Chromatografia jest szczególnie przydatna w analizach laboratoryjnych i badaniach jakościowych. W porównaniu do tych metod, destylacja jest bardziej efektywna w przypadku substancji o wyraźnie różniących się temperaturach wrzenia i znajduje szerokie zastosowanie w przemyśle chemicznym oraz farmaceutycznym.
Jakie są nowoczesne technologie stosowane w destylacji
W ostatnich latach nastąpił znaczny rozwój technologii związanych z procesem destylacji rozpuszczalników, co przyczyniło się do zwiększenia efektywności i bezpieczeństwa tych operacji. Nowoczesne aparaty destylacyjne często wyposażone są w zaawansowane systemy automatyzacji, które umożliwiają precyzyjne monitorowanie parametrów takich jak temperatura czy ciśnienie w czasie rzeczywistym. Dzięki temu możliwe jest szybkie reagowanie na zmiany warunków procesowych oraz minimalizacja ryzyka wystąpienia awarii. Ponadto rozwój materiałów konstrukcyjnych pozwolił na budowę bardziej odpornych na wysokie temperatury i korozję urządzeń destylacyjnych. Wprowadzenie technologii membranowych oraz mikrofalowych również otworzyło nowe możliwości w zakresie separacji składników chemicznych. Metody te mogą być stosowane jako alternatywa dla tradycyjnej destylacji lub jako jej uzupełnienie, co pozwala na uzyskanie lepszej jakości produktów końcowych oraz zmniejszenie zużycia energii.
Jakie są perspektywy rozwoju technologii destylacyjnych
Perspektywy rozwoju technologii związanych z destylacją rozpuszczalników są obiecujące i wskazują na dalszy postęp w tej dziedzinie. W miarę jak rośnie zapotrzebowanie na czyste substancje chemiczne oraz ekologiczne metody produkcji, techniki destylacyjne będą musiały ewoluować, aby sprostać tym wymaganiom. Przykładem mogą być innowacje związane z wykorzystaniem energii odnawialnej w procesach destylacyjnych, co pozwoli na zmniejszenie śladu węglowego produkcji chemicznej. Również rozwój nanotechnologii otwiera nowe możliwości zastosowania materiałów o unikalnych właściwościach fizycznych w konstrukcji aparatów destylacyjnych, co może poprawić ich wydajność i trwałość. W przyszłości możemy również spodziewać się większej integracji procesów chemicznych z cyfryzacją i sztuczną inteligencją, co pozwoli na optymalizację procesów produkcyjnych oraz lepsze zarządzanie zasobami.
Jakie są najważniejsze aspekty bezpieczeństwa w destylacji
Bezpieczeństwo w procesie destylacji rozpuszczalników jest kluczowym zagadnieniem, które wymaga szczególnej uwagi ze strony operatorów oraz zarządzających zakładami chemicznymi. Przede wszystkim, należy zapewnić odpowiednią wentylację w pomieszczeniach, gdzie odbywa się destylacja, aby zminimalizować ryzyko gromadzenia się toksycznych oparów. Warto również stosować systemy detekcji gazów, które mogą szybko zidentyfikować niebezpieczne substancje w powietrzu. Kolejnym istotnym elementem jest regularne przeprowadzanie szkoleń dla pracowników, które powinny obejmować zarówno procedury operacyjne, jak i zasady postępowania w sytuacjach awaryjnych. Dodatkowo, aparatura destylacyjna powinna być regularnie kontrolowana i serwisowana, aby zapobiec awariom.