Destylator przemysłowy to urządzenie, które odgrywa kluczową rolę w procesach separacji cieczy na podstawie różnic w ich temperaturach wrzenia. W praktyce oznacza to, że destylatory są wykorzystywane do wydobywania czystych substancji z mieszanin, co jest niezwykle istotne w wielu branżach, takich jak chemia, farmacja czy przemysł spożywczy. Proces destylacji polega na podgrzewaniu cieczy do momentu, gdy zaczyna ona parować, a następnie schładzaniu pary, aby skondensować ją z powrotem do postaci cieczy. W destylatorze przemysłowym zastosowanie znajdują różne technologie, takie jak destylacja frakcyjna czy prosta, które pozwalają na uzyskanie wysokiej czystości produktów końcowych. Kluczowym elementem tego procesu jest kolumna destylacyjna, która zwiększa efektywność separacji poprzez wielokrotne skraplanie i parowanie cieczy. Dzięki temu możliwe jest uzyskanie różnych frakcji o odmiennych właściwościach fizykochemicznych.
Jakie są najczęstsze zastosowania destylatorów przemysłowych
Destylatory przemysłowe znajdują szerokie zastosowanie w różnych gałęziach przemysłu, co czyni je niezbędnym narzędziem w wielu procesach produkcyjnych. Jednym z najważniejszych obszarów ich użycia jest przemysł chemiczny, gdzie służą do oczyszczania i separacji surowców chemicznych oraz produktów końcowych. Destylacja jest również kluczowym procesem w produkcji alkoholu, gdzie wykorzystywana jest do uzyskiwania wysokoprocentowych napojów alkoholowych poprzez oddzielanie etanolu od innych składników. W przemyśle petrochemicznym destylatory są używane do rozdzielania różnych frakcji ropy naftowej, co pozwala na uzyskanie benzyny, oleju napędowego oraz innych produktów naftowych. Kolejnym istotnym zastosowaniem jest przemysł farmaceutyczny, gdzie destylacja jest wykorzystywana do produkcji czystych substancji czynnych oraz rozpuszczalników. Ponadto destylatory znajdują zastosowanie w przemyśle spożywczym do produkcji olejków eterycznych oraz aromatów.
Jakie są różnice między różnymi typami destylatorów
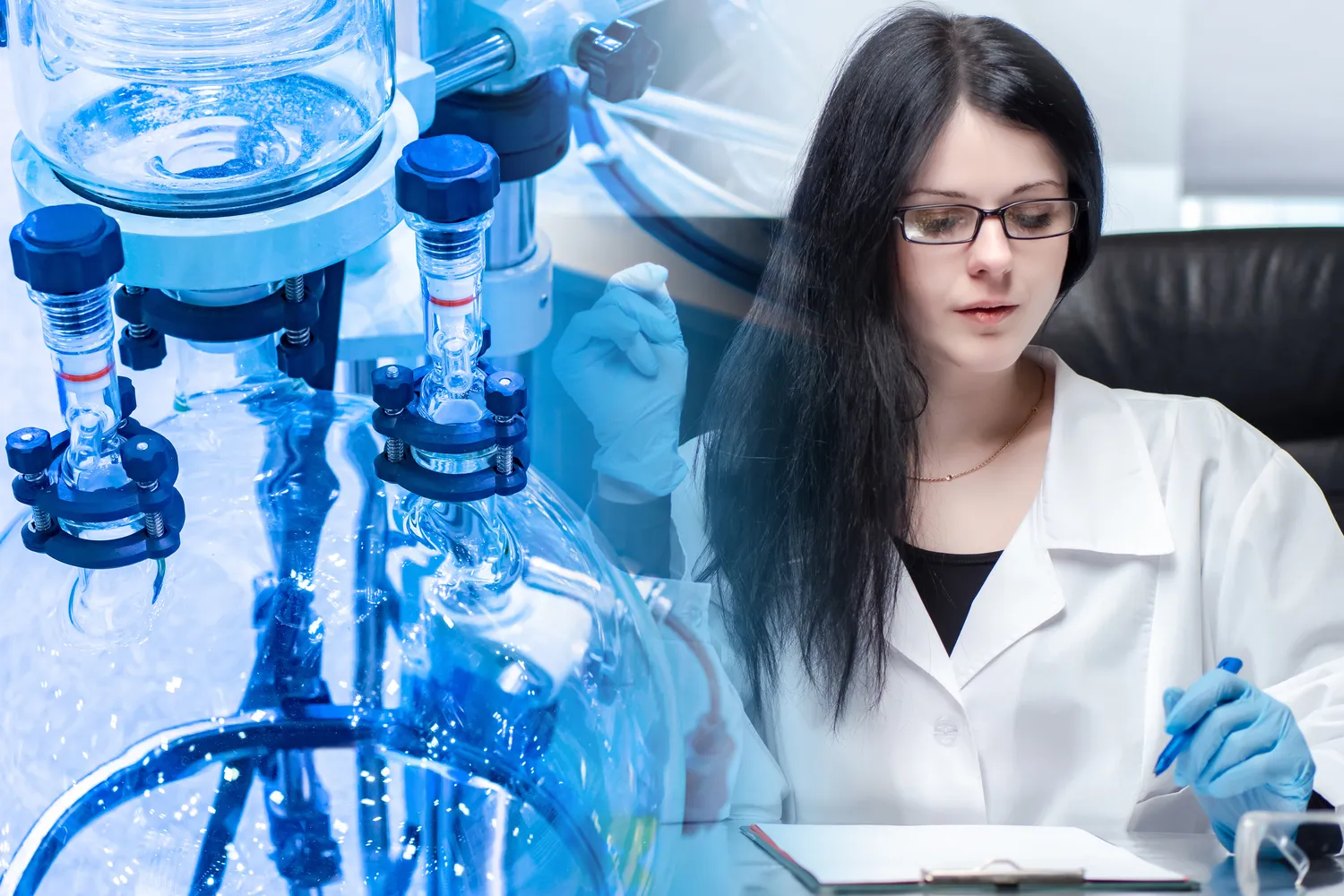
W świecie destylacji istnieje wiele różnych typów destylatorów, które różnią się zarówno konstrukcją, jak i zastosowaniem. Najpopularniejsze z nich to destylatory proste i frakcyjne. Destylatory proste są stosunkowo łatwe w budowie i działają na zasadzie jednego cyklu podgrzewania i skraplania cieczy. Są one idealne do separacji substancji o znacznej różnicy temperatur wrzenia. Z kolei destylatory frakcyjne są bardziej skomplikowane i wyposażone w kolumny destylacyjne, które umożliwiają wielokrotne parowanie i skraplanie cieczy. Dzięki temu można uzyskać bardziej złożone separacje i wyższe czystości produktów końcowych. Inne typy to destylatory próżniowe, które działają w obniżonym ciśnieniu, co pozwala na destylację substancji w niższych temperaturach, minimalizując ryzyko degradacji termicznej. Istnieją także destylatory azeotropowe, które umożliwiają separację mieszanin azeotropowych poprzez dodanie odpowiednich rozpuszczalników.
Jakie są koszty eksploatacji destylatora przemysłowego
Koszty eksploatacji destylatora przemysłowego mogą być znaczące i zależą od wielu czynników związanych z jego użytkowaniem oraz specyfiką procesu produkcyjnego. Przede wszystkim należy uwzględnić koszty energii potrzebnej do podgrzewania cieczy oraz chłodzenia pary podczas procesu destylacji. W przypadku dużych instalacji przemysłowych zużycie energii może być jednym z głównych wydatków operacyjnych. Kolejnym istotnym elementem kosztów są materiały eksploatacyjne oraz konserwacja urządzenia. Regularne przeglądy techniczne oraz wymiana części mogą generować dodatkowe wydatki, które należy brać pod uwagę przy planowaniu budżetu. Warto także zwrócić uwagę na koszty związane z zakupem surowców oraz ewentualnymi stratami materiałowymi podczas procesu produkcji. Efektywność działania destylatora ma bezpośredni wpływ na rentowność całego przedsięwzięcia, dlatego inwestycja w nowoczesne technologie oraz automatyzację może przynieść oszczędności w dłuższym okresie czasu.
Jakie są zalety posiadania nowoczesnego destylatora przemysłowego
Posiadanie nowoczesnego destylatora przemysłowego wiąże się z wieloma korzyściami, które mogą znacząco wpłynąć na efektywność procesów produkcyjnych oraz jakość finalnych produktów. Jedną z głównych zalet jest zwiększona wydajność procesu destylacji dzięki zastosowaniu zaawansowanych technologii i automatyzacji. Nowoczesne urządzenia często wyposażone są w systemy monitorowania parametrów pracy oraz algorytmy optymalizacji procesów, co pozwala na osiągnięcie lepszych wyników przy mniejszym zużyciu energii i surowców. Kolejną istotną korzyścią jest możliwość uzyskania wyższej czystości produktów końcowych dzięki zastosowaniu bardziej skomplikowanych procesów separacyjnych, takich jak destylacja frakcyjna czy próżniowa. Nowoczesne destylatory charakteryzują się także większą elastycznością w zakresie obsługi różnych rodzajów surowców oraz zmieniających się warunków produkcyjnych. Dodatkowo inwestycja w nowoczesny sprzęt może przyczynić się do poprawy bezpieczeństwa pracy dzięki zastosowaniu innowacyjnych rozwiązań technologicznych minimalizujących ryzyko awarii czy wycieków substancji chemicznych.
Jakie są kluczowe elementy konstrukcyjne destylatora przemysłowego
Kluczowe elementy konstrukcyjne destylatora przemysłowego mają ogromne znaczenie dla jego efektywności i wydajności. Podstawowym komponentem jest zbiornik, w którym odbywa się podgrzewanie cieczy. Zbiornik ten musi być wykonany z materiałów odpornych na działanie wysokich temperatur oraz chemikaliów, co zapewnia długotrwałą eksploatację. Kolejnym istotnym elementem jest kolumna destylacyjna, która umożliwia separację różnych frakcji cieczy. W kolumnach tych znajdują się różnego rodzaju wypełnienia lub talerze, które zwiększają powierzchnię kontaktu między parą a cieczą, co sprzyja efektywnemu procesowi skraplania i parowania. Ważnym aspektem jest również system chłodzenia, który odpowiada za kondensację pary z powrotem do postaci cieczy. Chłodnice mogą mieć różne formy, w tym chłodnice rurowe czy płytowe, w zależności od wymagań procesu. Dodatkowo, nowoczesne destylatory często wyposażone są w czujniki i systemy automatyzacji, które monitorują parametry pracy, takie jak temperatura, ciśnienie czy przepływ, co pozwala na optymalizację procesu i zwiększenie bezpieczeństwa operacji.
Jakie są najnowsze technologie w dziedzinie destylacji przemysłowej
Najnowsze technologie w dziedzinie destylacji przemysłowej przynoszą wiele innowacji, które mają na celu zwiększenie efektywności procesów oraz poprawę jakości produktów końcowych. Jedną z takich technologii jest zastosowanie membran w procesach separacyjnych, które pozwalają na selektywne oddzielanie substancji na podstawie ich wielkości cząsteczkowej lub właściwości chemicznych. Membranowe systemy separacyjne mogą być stosowane jako uzupełnienie tradycyjnych metod destylacji, co pozwala na osiągnięcie lepszych wyników przy niższych kosztach energetycznych. Innym nowoczesnym rozwiązaniem są destylatory z zastosowaniem technologii mikrofalowej, które umożliwiają szybkie podgrzewanie cieczy i skracają czas procesu destylacji. Dzięki temu możliwe jest uzyskanie wyższej jakości produktów oraz zmniejszenie zużycia energii. Warto również wspomnieć o automatyzacji procesów destylacyjnych, która staje się coraz bardziej powszechna w przemyśle. Systemy automatycznego sterowania pozwalają na precyzyjne monitorowanie i regulowanie parametrów pracy destylatora, co przekłada się na większą stabilność procesu oraz lepszą jakość finalnych produktów.
Jakie są wymagania dotyczące bezpieczeństwa w pracy z destylatorami
Wymagania dotyczące bezpieczeństwa w pracy z destylatorami przemysłowymi są niezwykle istotne ze względu na potencjalne zagrożenia związane z obsługą tych urządzeń. Przede wszystkim pracownicy powinni być odpowiednio przeszkoleni w zakresie obsługi destylatorów oraz znajomości procedur awaryjnych. Niezbędne jest również stosowanie odpowiednich środków ochrony osobistej, takich jak rękawice, gogle ochronne czy odzież odporną na działanie chemikaliów. Kolejnym ważnym aspektem jest regularne przeprowadzanie przeglądów technicznych oraz konserwacji urządzeń, co pozwala na wykrycie ewentualnych usterek przed ich wystąpieniem. W kontekście bezpieczeństwa istotne jest także zapewnienie odpowiedniej wentylacji w pomieszczeniach, gdzie znajdują się destylatory, aby uniknąć gromadzenia się niebezpiecznych oparów chemicznych. Dodatkowo należy przestrzegać norm dotyczących składowania substancji łatwopalnych oraz chemikaliów używanych w procesie destylacji. W przypadku awarii lub incydentu konieczne jest posiadanie planu ewakuacyjnego oraz procedur postępowania w sytuacjach kryzysowych.
Jakie są trendy rozwoju rynku destylatorów przemysłowych
Rynek destylatorów przemysłowych przechodzi dynamiczne zmiany związane z rosnącymi wymaganiami klientów oraz postępem technologicznym. Jednym z głównych trendów jest coraz większe zainteresowanie ekologicznymi rozwiązaniami, które pozwalają na zmniejszenie wpływu procesów produkcyjnych na środowisko naturalne. Producenci destylatorów starają się wdrażać technologie minimalizujące zużycie energii oraz surowców, a także ograniczające emisję szkodliwych substancji do atmosfery. Kolejnym istotnym trendem jest automatyzacja procesów produkcyjnych, która pozwala na zwiększenie efektywności operacyjnej oraz poprawę jakości produktów końcowych. Wprowadzenie systemów monitorowania i zarządzania procesami produkcyjnymi staje się standardem w nowoczesnych zakładach przemysłowych. Również rozwój technologii cyfrowych wpływa na rynek destylatorów; coraz więcej firm korzysta z rozwiązań opartych na sztucznej inteligencji i analizie danych do optymalizacji swoich procesów produkcyjnych. Dodatkowo rośnie zainteresowanie rynkiem małych i średnich instalacji destylacyjnych, które mogą być stosowane w lokalnych przedsiębiorstwach oraz startupach zajmujących się produkcją alkoholu czy olejków eterycznych.
Jakie są wyzwania związane z użytkowaniem destylatorów przemysłowych
Użytkowanie destylatorów przemysłowych wiąże się z różnymi wyzwaniami, które mogą wpłynąć na efektywność procesów produkcyjnych oraz jakość finalnych produktów. Jednym z głównych problemów jest konieczność ciągłego monitorowania parametrów pracy urządzenia, takich jak temperatura czy ciśnienie, co wymaga zaawansowanych systemów kontrolnych oraz wykwalifikowanego personelu. Ponadto zmienność surowców może prowadzić do trudności w utrzymaniu stałej jakości produktów końcowych; różnice w składzie chemicznym surowców mogą wpływać na efektywność procesu separacji i czystość uzyskanych frakcji. Kolejnym wyzwaniem są koszty eksploatacyjne związane z energią oraz materiałami eksploatacyjnymi; wzrost cen energii może znacząco wpłynąć na rentowność całego procesu produkcyjnego. Dodatkowo konieczność przestrzegania norm bezpieczeństwa oraz ochrony środowiska może wiązać się z dodatkowymi wydatkami związanymi z wdrażaniem odpowiednich procedur i technologii.